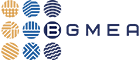
Charles Darwin said in his famous book “On the Origin of the Species” that it’s not the strongest or most intelligent of the species that survives but the one that’s most adaptable to change.
We may find a reflection of this aspect of Darwinism in the readymade garments industry of Bangladesh which has gone through an extraordinary level of transformation in the last four decades of its eventful journey.
The world of the clothing industry is ruled by consumer mindset, and it changes rapidly. However, the RMG sector had to change not only to catch up with the ever-evolving fashion and technology trends, but also to comply with international business standards and labor policy, and also to fulfill the expectations of more ethical, more environmentally-conscious brands and consumers.
Thanks to its high level of adaptability, today Bangladesh’s RMG industry can boast of having been transformed into a state-of-the-art, safe, secured and green hub of sustainable and ethical manufacturing.
The tremendous change that took place in the RMG industry has propelled Bangladesh to become the second largest garment exporter of the world, defying all odds and proving naysayers wrong who were busy writing epitaph for this sector.
The sector insiders’ relentless pursuit for staying competitive in the global supply chain has helped the industry make great strides in safety and sustainability which has drawn worldwide attention.
A recent survey report unveiled by Hong Kong-based supply chain compliance solutions provider, QIMA, ranked Bangladesh second in “Ethical Manufacturing” with a score of 7.7 only behind Taiwan which scored 8.0. Vietnam came in third, followed by Thailand, Pakistan, Turkey, China, India and Brazil.
The ethical auditing report covered a vast horizon of compliance and ethical manufacturing i.e. hygiene, health and safety, waste management, child and young labor, labor practices, including forced labor, worker representation, disciplinary practices and discrimination, Working hours and wages etc.
By comparing the ethical auditing practices of major manufacturing countries, QIMA noted that Bangladesh stood out for the good practices of its local suppliers in the international supply chain. This recognition from a globally acclaimed organization carries pride, prestige and joy for Bangladesh.
The practice of ethical manufacturing has boomed in Bangladeshi factories riding on the back of the interest of consumers and brands.
Ethical manufacturing is all about ensuring workplace safety, paying workers fairly, and being energy efficient and eco-friendly in the manufacturing process.
It gained popularity following a type of consumer activism called ethical consumerism that calls for boycotting products whose manufacturing process harms the environment or exploits workers. The latest QIMA report reflects that Bangladesh has made its mark in sustainable and ethical manufacturing.
However, it didn’t happen overnight. There lies a resounding success story behind this achievement, and we can understand it by looking back at the industry’s roller-coaster ride.
Starting its journey in an unplanned way in the early 1980s, the apparel sector started undergoing transformation in early 1990s. In the early phase of transformation, the issue of compliance to rules and regulations of global trading and supply chain has come to the fore. After the first decade, the factories in their increasing numbers have started moving from their unplanned facilities to safe facilities with sound structural design, which helped them increase their market share considerably.
Then in mid-1990s, the RMG industry addressed the issue of child labor. Before the enactment of The Child Labor Deterrent Act of 1993 tabled in USA Senate by Senator Tom Harkin, the issue of child labor did not receive that much attention. So, in the mid-1990s the leaders of the Bangladesh apparel industry extended full cooperation to the ILO, Bangladesh government and different NGOs such as BRAC and Gono Sahajjo Sangstha to deal with this issue.
Child laborers from factories were enrolled in NGO-run schools under the “earn and learn” scheme. In this process child labor was eradicated from factories through rehabilitation.
After that the whole industry has been brought under strict monitoring so that no factories can employ child laborer. As a result, the sector is totally free from child labor, which is evident in various local and international survey reports.
After successfully eliminating child labor, the factory owners started paying more attention towards issues related to social compliance. This includes complying with the buyers’ code of conduct as well as the labor law of the country, and fixation of minimum wage at regular intervals and full implementation of it.
In the aftermath of the Rana Plaza disaster, the sector has re-doubled its efforts to ensure safety, dignity and empowerment of the workers. The tragedy was in fact a major wakeup call and the way the industry has responded to remediate factories and made the workplace safer is remarkable.
The government has taken all-out efforts to bring legal reforms and strengthen the administrative capacity, which includes amendment to the Labor Act in 2013 and in 2018, promulgation of the Labor Rules in 2015, mandatory formation of safety committee and elected participation committee in every factory, the registration process of trade union has been made simpler.
Realising the importance of structural and electrical safety at factories in addition to fire safety, a National Tripartite Plan of Action was formed supported by ILO.
To complement the initiative, buyers came up and formed two private initiatives – Accord and Alliance – and through the collaborative efforts nearly 4000 factories were audited and remediated transparently with the support of national and international experts. Inspection reports of all factories are available in the websites of Accord and Alliance. This is how transparent it is.
Now the industry is under close surveillance of multiple authorities to ensure social compliance. In addition to the regular inspection by government-run DIFE, the Social Compliance Forum under the Ministry of Commerce regularly monitors compliance issues.
The industry associations and buyers’ nominated third party auditors also keep eyes on these issues. So the industry is quite open and transparent on compliance issues. A good number of the factories are also monitored by ILO Better Works.
Moreover, to carry forward the safety upgrade that has been achieved through Accord and Alliance, RMG Sustainability Council (RSC) has been formed involving equal numbers of representatives of industry bodies, brands and unions.
Through all these efforts, the industry has reached a height of standard which is unparalleled in terms of safety and transparency, and it is evident in the QIMA report.
A recent McKinsey report also dubbed Bangladesh’s RMG sector as “a frontrunner in transparency regarding factory safety and value-chain responsibility, thanks to initiatives launched in the aftermath of the disasters.” Mckinsey also highlighted the fact that more than 1,500 Bangladeshi companies are certified by the Global Organic Textile Standard, which is the second highest number in any country in the world.
Today the factories are not only safer, but also have become more dynamic, modern, energy-efficient and environment-friendly.
Bangladesh has by far the highest number of green garment factories in the world. US Green Building Council (USGBC) certified a total of 143 Bangladeshi factories as LEED (Leadership in Energy and Environmental Design), among them 40 are LEED platinum-rated and 89 are LEED gold-rated units.
Moreover, 500 more factories are in the pipeline for certification. It is also noteworthy to mention here that 39 out of the world's top 100 LEED factories are located in Bangladesh.
Besides, BGMEA, being the apex trade body of Bangladesh RMG industry, has joined the UN Fashion Industry Charter on Climate Action of the UNFCCC (United Nations Framework Convention on Climate Change).
BGMEA has also pledged to the German government-led global initiative named “Green Button”. Moreover, BGMEA has partnered with Global Fashion Agenda (GFA) and the Reverse Resources to build Circular Fashion Partnership (CFP) to initiate a circular business model in the industry. All these efforts testify to the industry’s strategic vision and commitment to environmental sustainability.
In a word, the readymade garment industry of Bangladesh has come a long way. But the industry is not letting complacency and inertia set in because the stakeholders are well aware of the fact that the only constant in business is change.
Now the industry is focusing on building its own capacity to monitor workplace safety through a national safety regime. Formation of RSC is a part of that endeavor.
Now that Bangladesh’s RMG industry is coming of age and there are signs that it is well-positioned to capture a leadership position in apparel export, achieving its own capacity to lead the industry towards safety and sustainability is of paramount importance at this stage of its long journey.
Written by Faruque Hassan, President of BGMEA, the article was first published in the Dhaka Tribune.