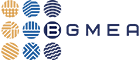
After the Savar’s Rana Plaza disaster and 1127 ready-made garments workers death in five garments factories located in the building there has been flurry of activities around the world, mostly condemning the Bangladesh Readymade Garments’ Manufacturers, the government and other relevant trade bodies for not overseeing the safety issues of approximately four million garments workers directly involved with the industry. Even the Pope in Vatican and our own Nobel Laureate Dr Muhammad Yunus went a step further and termed the RMG workers equivalent to slave labourers. Usually the Pope is not known to speak on such issues and the Nobel Laureate generally does not enter into debates on such national issues. It is good for us that they did, though I may have reservations about the comments of both, the Pope and the Nobel Laureate. The garments workers are neither slave workers nor even bonded labourers, but they are simply underpaid and exploited both by the manufacturers (with exceptions) and the buyers, collectively. The entire issue went to such an extent that one of the largest retailer in Canada, Tristan Style posted a multi-coloured sign in front of their stores saying “‘There is nothing in this store ‘Made in Bangladesh’, but a lot ‘Made in Canada’” notwithstanding the fact that the company which commenced business in 1970 now has grown in shape and size, with profitability rising every year and 70% of garments sold in their store are imported from other countries, mostly from Bangladesh. More interestingly America’s prestigious daily Washington Post published a survey report prepared by the ‘World Value Survey’ and termed Canada as one of the most tolerant countries of the world, and to the surprise of everyone Bangladesh has been termed as second racist country after Hong Kong! If posting signs like the ones in front Trinstan is the symbol of tolerance than the definition of racism and tolerance has to be reframed. More of that in future.
Accidents in factories are not rare in countries which steps into the world of industrialisation. It was quite common in England after the Industrial Revolution (I/R) and the curse of I/R was the child labour and the squalor conditions of labourers’ habitat. The Savar tragedy is considered as the second worst industrial disaster in history, the first one being the Bhopal (MP, India) lethal gas leak disaster that took place on the night of December 2-3, 1984, in the Union Carbide Pesticide Plant (UCPL) in Bhopal. Official counts estimate about 4000 people died in their sleep when the deadly gas leak occurred while the unofficial figure puts the figure to 8000. A few more thousands were maimed for life and the victims were never properly compensated by the company. UCPL was a subsidiary of the American Company Union Carbide. In 1911 one hundred and forty-six workers were burnt to death in the New York’s Triangle Shirtwaist Plant and as recent as April 16, 2013, 15 people died when a fertilizer factory in West Texas exploded. The explosion damaged or destroyed 150 nearby buildings and homes. The deadly incident could not attract much of the US media’s attention, not even the local ones
Like Bangladesh, Texas is not a stranger to terrible accidents in the work place. The New York Times reported that Texas has more work place casualties than any other state in the country. During each of the past 10 years it has had more than 400 fatalities. But all this happenings and ‘oversights’ in Texas or any other place should not be taken as an excuse either for Savar type tragedy or Tazreen Garments type disaster. We need to mend our own fences. When such disasters happen not only the industry looks down the barrel of a gun but also the country’s image is at stake.
The emergence and rise of RMG industry in Bangladesh is little over three decades’ old. From a meagre export of US $ 1.2 million worth of export in 1978 today the industry brings in on an average of US $ 20 billion, consisting of 80% of Bangladesh’s export earnings. Today Bangladesh is the second largest manufacturer of garments in the world, after China. Many of the buyers who imported their apparels from China moved to Bangladesh because it was cheaper to buy from Bangladesh than from China. A country where the traditional place of women was in the kitchen and who were expected to produce a child annually now has the industry where amongst the 4 million workers directly involved with the industry about 80% are women. The industry has produced a generation of entrepreneurs who have managed to put up about 5400 factories, though all of them cannot be considered to have complied with the accepted safety standards. Amongst these 5400 factories about 50% are engaged as subcontractors of the big ones who are usually compliance factories. The compliance parametres are usually set by the buyers and the government of Bangladesh. Many buyers have their compliance inspectors sitting in Bangladesh who can visit any factory unannounced to see if any of the compliance standards have been compromised. Factories working as subcontractors employ about one million workers.
Cheapness has a price and Bangladesh has paid for it on number of occasions. In the market economy the buyer will always look where s/he can buy his goods one penny cheaper and though he will use price as a competitive advantage to attract his customers s/he will also have to compromise quite a few standard in his outlet, in terms of labour benefits, including their salary and wages. Take the example of Wal Mart, one of the largest buyers of apparels from Bangladesh. Though it is the largest retailer in the world at the same time is also considered by its employees as the worst company to work for. A few years back Andrew Gumbel writing for the daily Independent, UK, said: “There can be a few chief executives in corporate America more uncomfortable at the moment than Lee Scott of Wal-Mart. Not that he should necessarily have our sympathy: his company, known unaffectionately as the Beast of Bentonville, after its corporate home, is the biggest single private employer in the United States. Its network of more than 3,500 discount retail stores has been lambasted repeatedly in recent years for its rock-bottom wages, which oblige thousands of its lower-end employees to resort to government subsistence, including food stamps, to make ends meet. It has faced down critics for its reliance on overseas sweatshop labor, especially in China, to produce the goods with which it stocks its shelves. It has met community resistance to new store openings in many parts of the country because of its tendency to empty town centres of traditional family-owned businesses and foster suburban sprawl. It has been accused, in fact, of being the very emblem of everything that assails the modern American economy, as old-style industrial manufacturing jobs are outsourced overseas and are replaced with low-wage, low-security service-sector work.” (November 2, 2005). Things have not changed since then and same is true for other importers like the Macys, K-Mart, J C Penny and few others.
There is no denying the fact that the Bangladesh’s RMG sector is in a messy situation. For sometimes US has been threatening that it will withdraw the GSP facilities (US Generalised System of Preference) given to Bangladesh, though this privilege given to our garments export is insignificant. It tried to tie TICFA (Trade and Investment Cooperation Framework Agreement) with GSP. The controversial TICFA has been around for a few years in Bangladesh in some form or other, but so far has not been signed. Analysts say it is an unequal agreement whose balance will be tilted towards US. Recently our Foreign Minister Dr Dipu Moni announced that the agreement will be signed soon, and the interest of Bangladesh will be protected. However the contents of the agreement are yet to be known. US pushes to give the garments workers right to form Trade Unions and raise the minimum wages though it refuses to give Bangladesh apparels duty free access to its markets though it is given to products from Vietnam, Cambodia or Columbia. Ironically Bangladesh pays highest duty for its garments export to US. While Bangladesh pays 15.3%, China, a developed country, pays only 3%.
There are dozens of prescriptions as how Bangladesh should get out of the present quagmire. Our own Noble Laureate has prescribed that the garments workers be given minimum international wages. It is more easily said done. The onus of agreeing on such minimum wages will surely lie not only on Bangladeshi manufacturers but also on the buyers. A Bangladeshi garment worker currently gets somewhere between 25 to 27 cents per hour. In our nearest rival Sri Lanka it is 45 cents while India is 55 cents. Labour cost is one of many factors that go into making apparels. There are costs of capital and raw materials, the efficiency of infrastructure and on top of everything the productivity of the workers. Almost all of our RMG sector workers are on-the-job trained and their efficiency is not upto the international level which is in contrast to the RMG sector in Sir Lanka where there are about 1000 training institutes to train would be workers in this sector.
The good news is that many importers, such as H&M, Benetton, Indetex, Carrefour, Marks & Spencer, El Corte Ingles, a total of 37 international companies, majority of them based in EU have signed an Accord to help Bangladesh Garments Manufacturers on Fire and Building Safety. All of these are EU based importers. The only US based importers so far to have signed are Abercombie & Fitch and PVH. Wal-Mart said it is non-committal and will work independently and so far has identified 300 factories with whom it will not place orders, a move not considered very judicious by industry analysts. Disney went a step further and pulled out from Bangladesh. The government of Bangladesh has announced it will review the minimum wages and has already drafted a new labour law which the labour leaders have said may not be acceptable to them because they were not discussed. The problem is that the labour leadership in the RMG sector has always been under shadow of doubt. Currently there are at least 60 self-styled labour unions in this sector and most leaders are accused of being self-seeking instead of looking at the interest of the labourers. The government must also do more like strengthening its inspection team visiting factories. The team should consist of independent members, like competent experts from BUET and other universities. The importers should be willing to pay a few cents extra for their imports and the manufacturers willing to take few cents less as profit. A proposal for establishing an internationally recognised accreditation body like we have for academic institutions, hospitals or hotels should be considered.
These days the entrepreneurs have other options for investment. RMG sector is a labour intensive sector and if they move away from this sector because the buyers are threatening to move away then the country will be thrown into a desperate unemployment situation, which in turn will trigger many social problems. The sector must be saved and it will need a collective effort of the government, manufacturers, employees and the importers. Turning away from Bangladesh will not solve the problems, rather they will be worsened. Let us have a win-win situation.
The writer is a former Vice-chancellor of Chittagong University. Currently he teaches at ULAB, Dhaka.