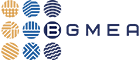
Faruque Hassan found himself in a sticky situation last month when his garment factory could not complete the orders. He still had 20 percent job to finish, but frequent power cuts and low gas pressure had eaten up his shipment time. Worst still, his buyer would not accept any partial shipment -- they want the whole lot in one go.
In the end, Faruque, owner of Shafi Processing Industries Ltd, sorted out his trouble in a costly way. He chartered a flight and sent his apparels. For this he had to pay Tk 6.5 crore from his own pocket as airfreight.
Faruque's case is all too similar to many garment owners' today. As power cuts have turned frequent too many times, and as gas pressure dipped, machines remain silent for hours in factories. Only last week, this newspaper ran a picture of Sinha Textile with its boilers sitting idle with its workers. In the last one and a half months, about 100 chartered planes left Dhaka airport with shipments.
And each airfreight means loss for the exporters as they have to foot the bills from their pocket. Every kilogram of goods put on a plane costs $4.30, and the worst part is that the buyer would not pay for it. They would not even refund the shipment cost factored in the free on board (FOB).
To minimise their costs, exporters are now first shipping their goods to Singapore or Dubai and airlifting them from those business hubs. This minimises the loss in airfreight.
To make things worse, Bangladesh's productivity in the apparel sector has not improved, and remains at a much lower level compared to other competitors like China. Against Bangladesh's productivity of 35 percent, China's is about 80 percent, and major Southeast Asian countries' are in the 70 percent range.
There are a few factories which have opted for lean production style -- a process in which every work is calculated for time, and then the production line is put in place in a way that maximises the productivity of workers. This has improved their worker productivity to over 50 percent. But the story stops there.
Faruque said his factories saw a 20 percent slide in productivity. "I could produce 120 T-shirts per worker an hour. Now I can do hardly 100."
Frequent power cuts are a major reason for such a loss in productivity. Workers' lack of skill is also a reason. But the other major reason is that the manufacturers are producing more and more higher-priced products which require more designs. This is needed for fetching higher prices, but at a cost of productivity loss.
Right now, the country is reeling under power and gas crises, and no end is in view within the next few years. Different gas-fired power plants having around 800 megawatt power generation capacity have remained idle due to the gas crisis. This is intensifying the over-all power load shedding which tends to hover between 1,200 MW and 1,500 MW daily -- which is one third of the country's power demand.
The situation renders Bangladesh's garment industry uncompetitive. A static exchange rate for almost four years has not helped the export cause either.
These in balance leaves about 30 percent of the country's garment capacity idle, according to industry insiders. This means a lost case for 1 million workers.
The situation also does not bode well if laid in statistics. Apparel exports have been clocking negative growths for the last few months, despite Bangladesh today standing as the second largest garment exporter in terms of quantity.
From the beginning of this fiscal year in July, garment exports have been showing a continuous negative growth, a very unusual trend for the sector. In September, it dipped by a highest 29 percent. The chill intensifies as garment accounts for about 80 percent of the country's total exports.
Manufacturers find themselves in a tight corner as order prices are falling. But this is a natural process.
"Look at the television market. Price of a TV set has come down so dramatically. The same thing is also happening in the garment sector," said David Hasanat, chairman of Viyellatex. "But we have to increase our productivity to offset falling prices. This is the challenge."
But that challenge is now seriously threatened by frequent turnover of workers, and their poor quality. It is a constant uphill battle for factories to retain workers. Once workers come and get trained, every likelihood is that they will hop jobs.
"It is a regular feature," said Faruque adding, "With the payment of monthly salaries, we find a regular migration. When it happens we suffer in production."
In a lean production line, where every job is timed to the second, it leads to a snarl-up when even a few slow workers fail to keep up in the middle. And this is happening frequently, adding to the woes from the power outage and gas shortage.
"There is no dearth of orders. The question is, can we execute them?" said Abdus Salam Murshedy, president of Bangladesh Garment Manufacturers and Exporters Association. "We need to bag these orders because otherwise we will see more competitors springing up elsewhere in the world. And we need the orders to keep our idle capacity running. This would make the whole garment industry healthy."